The Only Guide for Alcast Company
The Only Guide for Alcast Company
Blog Article
Getting The Alcast Company To Work
Table of ContentsThe smart Trick of Alcast Company That Nobody is Talking AboutThe 6-Minute Rule for Alcast CompanyThe Best Strategy To Use For Alcast CompanyAbout Alcast CompanyMore About Alcast CompanyThe 7-Minute Rule for Alcast Company
Chemical Comparison of Cast Light weight aluminum Alloys Silicon promotes castability by lowering the alloy's melting temperature level and enhancing fluidity during casting. In addition, silicon adds to the alloy's strength and wear resistance, making it valuable in applications where resilience is important, such as vehicle components and engine parts.It additionally enhances the machinability of the alloy, making it much easier to process right into ended up products. In this means, iron adds to the total workability of aluminum alloys.
Manganese adds to the toughness of aluminum alloys and enhances workability (aluminum foundry). It is typically used in wrought light weight aluminum products like sheets, extrusions, and profiles. The presence of manganese aids in the alloy's formability and resistance to breaking throughout construction processes. Magnesium is a lightweight component that offers toughness and effect resistance to light weight aluminum alloys.
Some Known Details About Alcast Company
It permits the production of lightweight parts with outstanding mechanical homes. Zinc enhances the castability of light weight aluminum alloys and assists manage the solidification procedure throughout spreading. It enhances the alloy's toughness and hardness. It is typically located in applications where elaborate shapes and fine information are required, such as decorative spreadings and specific vehicle parts.
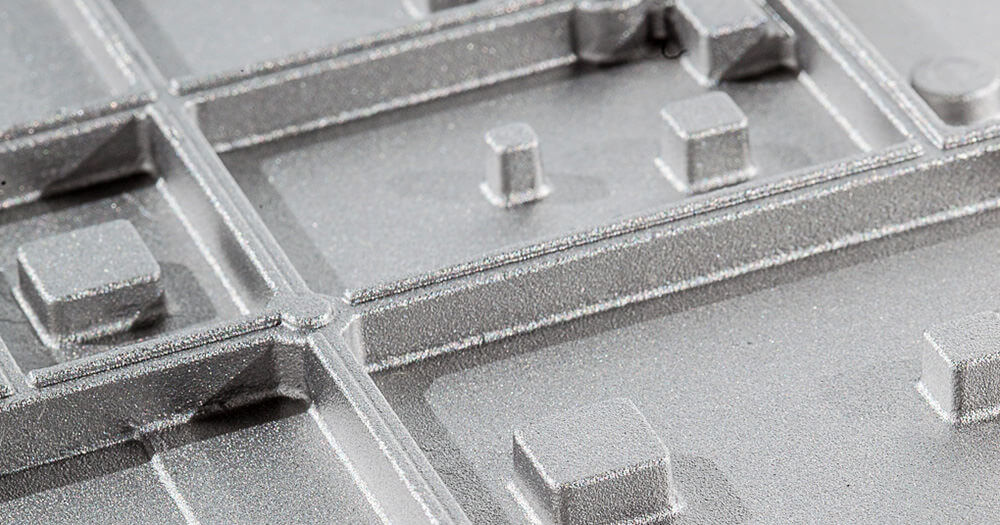
The main thermal conductivity, tensile toughness, yield stamina, and elongation vary. Select ideal basic materials according to the efficiency of the target item generated. Among the above alloys, A356 has the highest thermal conductivity, and A380 and ADC12 have the most affordable. The tensile limitation is the opposite. A360 has the very best yield stamina and the highest elongation rate.
See This Report on Alcast Company
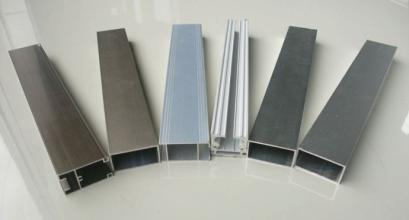
In precision spreading, 6063 is fit for applications where intricate geometries and high-quality surface finishes are paramount. Instances consist of telecommunication units, where the alloy's superior formability permits streamlined and visually pleasing styles while maintaining structural honesty. Similarly, in the Lighting Solutions market, precision-cast 6063 parts create elegant and efficient lights components that require detailed shapes and great thermal efficiency.
It results in a better surface area coating and much better deterioration resistance in A360. Additionally, the A360 shows premium prolongation, making it perfect for complex and thin-walled elements. In precision spreading applications, A360 is well-suited for industries such as Consumer Electronic Devices, Telecommunication, and Power Devices. Its improved fluidity permits complex, high-precision components like mobile phone housings and communication Click This Link gadget housings.
Some Known Questions About Alcast Company.
Its special residential properties make A360 an important selection for accuracy spreading in these markets, boosting item longevity and high quality. Aluminum Casting. Light weight aluminum alloy 380, or A380, is a commonly utilized casting alloy with a number of unique attributes.
In precision casting, light weight aluminum 413 beams in the Consumer Electronic Devices and Power Devices sectors. It's generally utilized to craft intricate elements like mobile phone real estates, cam bodies, and power device cases. Its accuracy is exceptional, with limited resistances approximately 0.01 mm, making certain flawless product setting up. This alloy's remarkable rust resistance makes it an outstanding choice for outside applications, ensuring lasting, long lasting items in the mentioned sectors.
All about Alcast Company
As soon as you have determined that the aluminum die casting procedure appropriates for your task, a crucial next action is selecting the most appropriate alloy. The light weight aluminum alloy you select will considerably influence both the spreading procedure and the homes of the end product. As a result of this, you need to make your decision meticulously and take an enlightened approach.
Determining the most suitable aluminum alloy for your application will certainly imply considering a wide variety of attributes. The initial classification addresses alloy characteristics that impact the manufacturing procedure.
The smart Trick of Alcast Company That Nobody is Discussing
The alloy you select for die spreading straight affects numerous elements of the spreading process, like exactly how simple the alloy is to deal with and if it is susceptible to casting defects. Warm cracking, additionally called solidification splitting, is a common die spreading issue for aluminum alloys that can cause interior or surface-level rips or cracks.
Particular light weight aluminum alloys are extra vulnerable to warm breaking than others, and your selection should consider this. An additional common issue located in the die spreading of aluminum is die soldering, which is when the cast stays with the die wall surfaces and makes ejection challenging. It can damage both the actors and the die, so you need to seek alloys with high anti-soldering homes.
Deterioration resistance, which is already a notable feature of aluminum, can vary considerably from alloy to alloy and is an important characteristic to take into consideration relying on the environmental conditions your item will certainly be exposed to (aluminum casting company). Wear resistance is one more residential or commercial property generally looked for in light weight aluminum products and can differentiate some alloys
Report this page